Decarbonising steelmaking with BioIronTM
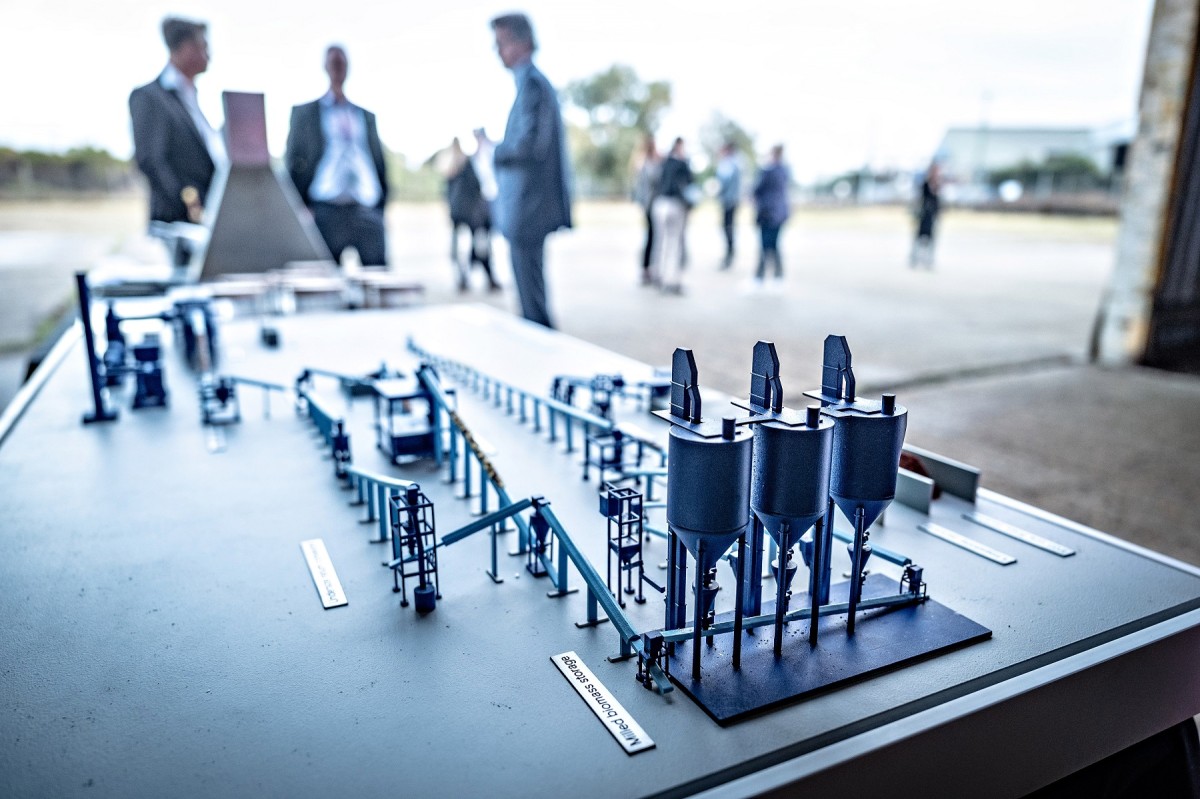
Steel is one of the most important and commonly manufacturered materials in the world and turning iron ore into steel is an energy intensive process that accounts for around 7% to 9% of the world’s global CO2 emissions.
As one of the world’s largest iron ore producers, Rio Tinto (ASX: RIO) is aiming to find more sustainable ways to produce steel whilst meeting climate objectives and reducing emissions.
It’s doing this by exploring three different pathways: lowering the carbon impact of existing blast furnace technologies; speeding up emerging technologies; and researching innovative low CO2 technologies.
One of Rio’s most promising options is BioIronTM.
What is BioIronTM?
Traditionally, iron ore and coking coal are processed and charged into a blast furnace. Hot air at around 1200°C is blown in, causing the coking coal to react with the iron ore and create pig iron.
This step alone emits 2t of CO2 per tonne of steel output.
BioIronTM uses raw biomass, such as agricultural waste, as a reductant instead of coal and microwaves powered by electricity to reach temperatures needed to turn the ore into metallic iron.
The biomass provides most of the energy needed so the BioIronTM processes uses less than one-third of the electricity needed compared to other new technologies which use hydrogen.
To make BioIronTM, Rio blends fine Pilbara iron ore and fine biomass with fluxes and feeds the combined product into a high pressure machine to produce briquettes – which are roughly the size of golf balls.
The briquettes are then layered on a high temperature conveyor belt where biomass gases combust with air to heat the briquettes.
Once the bed has reached 600°C, the briquettes transition to the microwave section of the furnace.
In the microwave section of the furnace, the briquettes absorb the microwave energy and turn into highly metalised direct reduced iron.
These microwaves heat the whole bed depth, which is a unique and efficient feature that hasn’t been achieved to date by conventional technologies.
An electric melter then separates impurities from the hot metal which can either be fed into a basic oxygen furnace on site or cast into pig iron and transported to remote steelworks.
When combined with renewable energy and carbon-circulation by fast-growing biomass, BioIronTM has the potential to reduce carbon dioxide emissions by up to 95% compared to the current blast furnace method.
BioIronTM success
In November 2022, Rio confirmed the effectiveness of the BioIronTM process using ores from its mines in Australia in a small-scale pilot plant in Germany.
For over 18 months, the BioIronTM process was extensively tested by a project team from Rio, sustainable technology company Metso Corporation (formerly Metso Outotec) and the University of Nottingham’s Microwave Process Engineering Group.
Development work was conducted in a small-scale pilot plant using batches of 1000 golf ball-sized briquettes.
Rio chief commercial officer at the time Alf Barrios commented on the process.
“Finding low-carbon solutions for iron and steelmaking is critical for the world as we tackle the challenges of climate change,” he said.
“Proving BioIronTM works at this scale is an exciting development given the implications it could have for global decarbonisation.
“BioIronTM is just one of the pathways we are developing in our decarbonisation work with our customers, universities and industry to reduce carbon emissions right across the steel value chain.”
BioIronTM pilot plant
In mid June 2024, Rio announced it would be investing $215m (US$143m) to develop a research and development facility in WA to further assess the effectiveness of its BioIronTM process.
The development of the facility, which is located in the Rockingham strategic industrial area, followed the successful trials in Germany.
The pilot plant will be 10 times bigger than its predecessor and will be the first time the steelmaking process has been tested at a semi-industrial scale, capable of producing 1t of direct iron per hour.
The plant was designed in collaboration with the University of Nottingham, Metso Corporation and WA engineering company Sedgman Onyx.
make this a reality,” says Rio Tinto’s Simon Trott, pictured here in the foreground.
On the release of the announcement, Rio Tinto iron ore chief executive Simon Trott commented on the facility.
“The world needs low-carbon steel to reach net zero and we are working to make this a reality by finding better ways to turn our Pilbara ores into steel,” he said.
“BioIronTM is a world-first technology that has the potential to play a significant role in a low-carbon steel future.
“This research and development facility will further test the BioIronTM process, showcase WA innovation capability and further demonstrates Rio Tinto’s commitment to supporting and enabling the decarbonisation of the steel industry.”
Fabrication of the equipment will begin this year with commissioning expected in 2026.