Fortescue: Leading the green industrial revolution
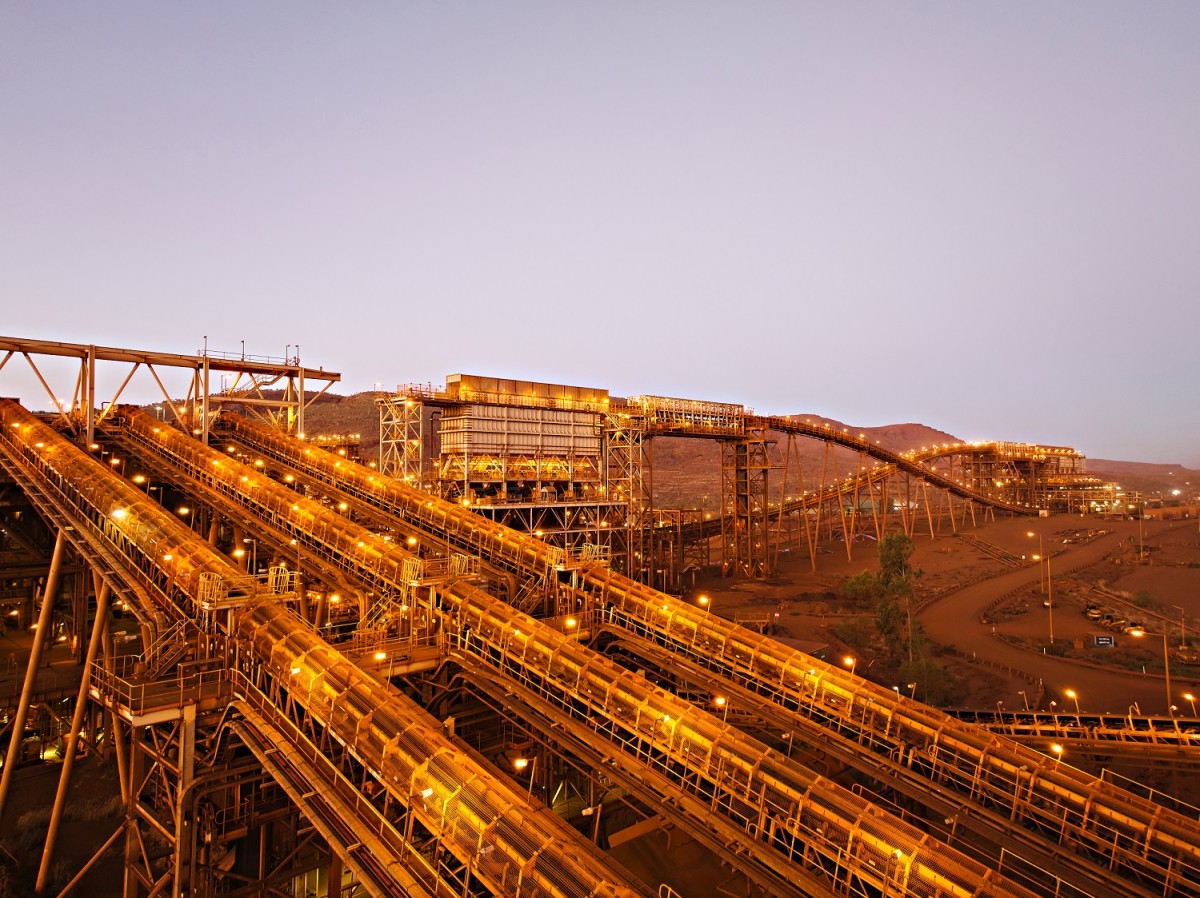
Since its founding 20 years ago, Fortescue (ASX: FMG) has become one of the world’s largest iron ore producers and is the country’s major supplier of iron ore to China’s steel industry.
Since its first shipment of iron ore departed Port Hedland, WA, to China in 2008, Fortescue now ships over 190mt of iron ore per year, with more than 2bt of iron ore delivered to its customers since its inception.
Fortescue’s iron ore operations include two hematite mining hubs in the Pilbara — Chichester Hub and Western Hub — and the Iron Bridge magnetite mine, all of which are in WA.
Operations
Chichester Hub
Fortescue’s Chichester Hub includes the Cloudbreak and Christmas Creek mines, and it has an annual production capacity of around 100mt from three ore processing facilities (OPFs).
The Christmas Creek OPF has been upgraded to include a wet high intensity magnetic separator to recover high-grade iron from the finer ore fed through the OPF.
“Christmas Creek is home to our Green Energy Hub and soon to be Green Metal project,” Fortescue chief executive Dino Otranto told the Australian Mining Review.
“A 60MW solar farm partly powers daytime operations at the Chichester Hub, displacing around 100ml of diesel every year.”
In mid-August, ground broke at the $75.4m (US$50m) Christmas Creek Green Metal project, a step towards developing a green iron industry in WA.
The project will produce iron using green hydrogen, which will be suitable for use in almost any steel plant across the globe.
It aims to produce green iron metal by the end of 2025, creating a catalyst for the next generation of Australia’s green iron industry.
Western Hub
Fortescue’s Western Hub contains two mines — Solomon and Eliwana — and together the mines have an annual production capacity of around 100mt.
Solomon began operations in 2012, while Eliwana opened in December 2020.
With its innovative low profile designed OPF and dual stacker reclaimer, Eliwana has the capacity to direct load onto trains up to 9000tpa.
Iron Bridge
Located 145km south of Port Hedland, Iron Bridge was Fortescue’s first magnetite operation, and it signified the company’s entry into the high-grade segment of the iron ore market.
Iron Bridge produces a wet concentrated product which is transported to Port Hedland through a 135km specialist slurry pipeline.
Over the coming years, low-cost power will be delivered to Iron Bridge through Fortescue’s investment in the Pilbara Energy Connect project, which includes energy transmission line infrastructure, solar gas hybrid generation and an associated battery storage solution.
“Iron Bridge is our most innovative and complex iron ore project,” Mr Otranto said.
“It has an iron grade of over 68% and, once we connect it to Pilbara renewable energy, it will be Australia’s first magnetite project to operate using renewable energy by 2030.”
Iron Bridge is held in an unincorporated joint venture between FMG Magnetite (69%) and Formosa Steel (31%).
Sustainability efforts
By 2030, Fortescue aims to have its Australian iron ore operations running on green energy and achieve real zero terrestrial emissions (Scope 1 and 2).
Decarbonisation by 2030 will allow Fortescue to save over 700ml of diesel, 15mgj of gas and 3mt of CO2 equivalent emissions each year.
This will generate significant cost savings for Fortescue, with the company spending over $844m (US$560m) on diesel and gas in FY23.
Furthermore, to address emissions across its entire value chain, the company has a net zero Scope 3 emissions target by 2040.
Fortescue’s approach to reducing Scope 3 emissions is to develop projects and technologies with a focus on reducing emissions from iron and steelmaking.
“Our energy business is leading the green industrial revolution, building a global portfolio of renewable green hydrogen and green ammonia projects, and developing green technology solutions,” Mr Otranto said.
“Through Fortescue Zero, we are developing and manufacturing zero emissions battery systems, hydrogen production systems and technology that will help to decarbonise our own mining operations.
“Fortescue Zero is also developing and selling that technology to others to help them to join us in eliminating the use of fossil fuels globally.
“We will offer a diverse array of electrolyser products, systems and services, encompassing multiple cutting-edge technology types and membrane developments.”
Green ammonia and green hydrogen
In its journey to move beyond fossil fuels, Fortescue is creating new opportunities for green iron, green steel, green hydrogen and green ammonia.
Ammonia synthesis
“We believe battery electric, green hydrogen and green ammonia will all be critical to our decarbonisation plan, and we are taking practical steps to apply the best solution to each situation,” Mr Otranto said.
“Ammonia can be made synthetically by combining nitrogen with hydrogen, in a process called ammonia synthesis.
“When this process is completed using renewable energy sources such as wind, solar, hydropower, geothermal energy and zero carbon emissions, the result is green ammonia.
Hydrogen through electrolysis
“Although its supply is infinite, hydrogen is not commonly found in its pure form in nature. It can be manually produced through a process called electrolysis.
“This process requires electricity and when achieved using renewable energy resources like solar, wind, hydropower or geothermal energy, the result is green hydrogen.”
Green technologies
To meet these sustainability efforts, Fortescue has taken steps to decarbonise shipping and develop autonomous haulage solutions to deliver zero emissions autonomous haul trucks.
Ammonia-powered vessel
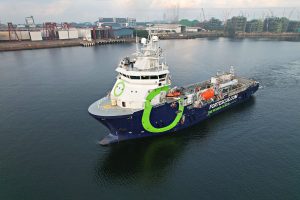
In mid-March 2024, Fortescue completed the world’s first use of ammonia, in combination with diesel in the combustion process, as a marine fuel onboard the Fortescue Green Pioneer in the Port of Singapore.
The Fortescue Green Pioneer began its journey towards becoming the world’s first ocean going ammonia-powered vessel in 2022 when Fortescue successfully converted a four stroke engine to run on ammonia, in combination with diesel, at its testing facility in Perth, WA.
A few months later, the vessel won the Hydrogen Transport award at the Sustainable Energy Council’s World Hydrogen 2024 Awards in Rotterdam, the Netherlands.
“In March 2024, the Fortescue Green Pioneer received the world’s first certification to use ammonia in combination with diesel as a marine fuel, bringing us one step closer to green shipping,” Mr Otranto said.
Fortescue then signed a non-binding Memorandum of Understanding with COSCO SHIPPING, with the two companies to work collaboratively on decarbonising shipping.
The companies will explore the construction and deployment of COSCO SHIPPING vessels, or co-owned vessels, powered by green ammonia to reduce shipping emissions between Australia and China.
“The shipping industry plays a vital role in global trade but also contributes significantly to the world’s carbon emissions,” Mr Otranto said.
“This collaboration marks a significant step in decarbonising the shipping industry and establishing a green fuel supply chain.
“It also paves the way for collaboration on a variety of decarbonisation solutions, which we believe will be integral to delivering on our ambitious target of net zero Scope 3 emissions by 2040.”
Hydrogen haul truck
Fortescue has also partnered with Liebherr Mining to develop and validate a fully integrated autonomous haulage solution (AHS) across its Australian iron ore operations.
The AHS integrates a Fleet Management System (FMS), onboard autonomy kit for the T 264 truck and a high precision machine guidance system for loading equipment.
The FMS has been designed to optimise fleet utilisation and maximise productivity, while maintaining efficient consumption of fuel and energy.
Europa, the hydrogen-powered haul truck prototype, is currently at the Christmas Creek mine in the Pilbara, and is undergoing site-based testing over the next few months.
Once commissioned on site, Europa will be refuelled with liquid hydrogen from a gaseous and liquid hydrogen plant at Fortescue’s Green Energy Hub.
“Europa is at Christmas Creek now for further site-based testing and commissioning. We will use the results from this testing to inform our future fleet of zero emissions trucks,” Mr Otranto said.
“Following the success of our battery electric haul truck prototype at site, we’re thrilled to now have Europa up and running on hydrogen.
“This is a huge achievement for the team and brings us another step closer to have a fleet of zero emissions trucks at our sites by the end of this decade.”