The next generation of modelling
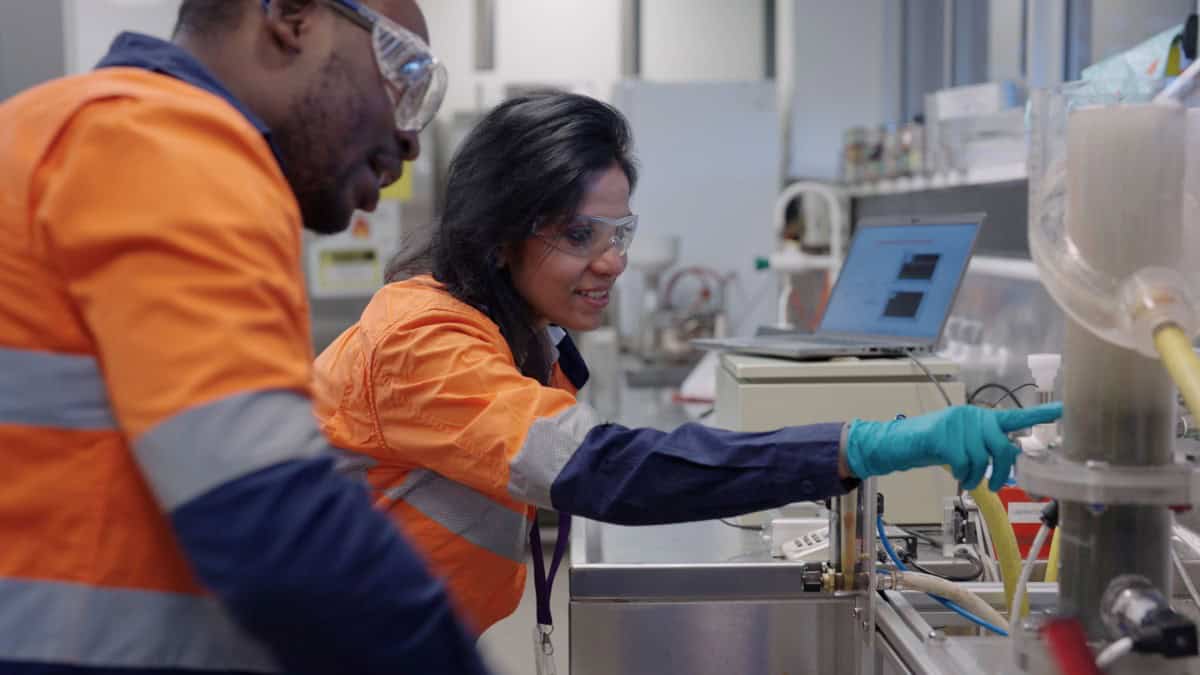
Mining companies have found themselves walking a tightrope, balancing the demand to quickly produce larger quantities of critical minerals for the energy transition while simultaneously finding ways to implement smarter and cleaner processes.
Although many new technologies have been developed over the last decade which promise less energy and water use, optimise performance and create an overall smaller footprint, mining companies still must front the cost and risk of adopting untested equipment that potentially doesn’t improve upon existing infrastructure.
As a result, the mining industry has become resistant to change, using the same mineral processing technologies for decades. This is largely due to a lag in evaluation capabilities that would protect mining companies from the risk of adopting experimental equipment.
As new equipment is developed, engineers need new methods of evaluation that will insulate them from financial risk while boosting production necessary for the energy transition.
The Australian Mining Review speaks with the The University of Queensland’s Sustainable Minerals Institute (UQ SMI) Separation Group lead Associate Professor Kym Runge about revolutionising model development for emerging mineral processing technology in the mining industry.
New generation modelling initiative

The Separation Group at UQ SMI has proposed a novel approach to modelling which would prime the mining industry for innovation by allowing for more efficient and scalable model development for emerging mineral processing equipment. Advanced modelling can be used by researchers and engineers to trial equipment before mining companies front the cost of adopting new technologies on site.
Historically, the mining industry has utilised a model reliant on hundreds of physical experiments and interpretation of data trends. This method has proven cumbersome, requiring many physical experiments to run on each new type of equipment and then waiting for researchers to interpret results before developing a traditional simulation model. This is time consuming and expensive, as it requires large pieces of equipment to be fully built and must account for lengthy testing periods.
Dr Runge says UQ SMI is innovating a new approach that is faster and more flexible. The new approach employs a physics-based model that utilises universal laws of nature to simulate the physics of systems, allowing for adaptive modelling.
“In the past what we have done is really just gone out and done experiments on things and then tried to piece together a model that we thought would work,” she said.
“We try lots of different models and their simplifications of the process and we see if we can get it to match. Sometimes that works, sometimes it doesn’t.
“This computational fluid dynamics (CFD) model is a different approach where we will be fundamentally simulating the physics of the system that breaks it down into lots and lots of little components and calculates the physics and then how those all interact together to ultimately predict how the equipment or system performs.”
The new generation modelling initiative would require fewer physical experiments by using the CFD to support fundamental knowledge development and improved equipment modelling.
UQ SMI has already completed experiments that serve as a knowledge base for the CFD to evolve from. Although the mining industry has been jolted by sweeping innovations, the new technologies are mostly slight variations of existing designs. Using this as an advantage, the CFD will simulate the physics of the equipment to test the slight alterations that potentially increase efficiency and reduce emissions.
The CFD uses physics packages that have been developed over years from other industries. Key physics likely to drive the process can be selected from these packages and tested in the CFD. This will identify the essential physics to be incorporated into the equipment models.
Once these models have run, they can be compared to the experimental data to determine if the physics has been captured correctly. With this method, equipment models do not have to be pieced together because they are developed based on an understanding of the essential physics involved.
On site applications
Small changes to equipment can make big differences in efficiency on site. In addition to testing the feasibility of emerging technologies, the CFD can be used for on site equipment optimisation, scaling and development of process control systems.
Dr Runge says the CFD will enable engineers to assess the benefits of adjustments.
“If you look at most of the equipment it’s just different combinations of the same thing, put together in different ways,” she said.
“The later models will be much easier to develop than the ones we are developing now, and once we develop the models, we can use them for so many different things.
“You can look at scaling from small scale to large scale. It’s all the same physics, so it will work. We can use it to say what’s the best size of this equipment.”
Rather than mining companies making time consuming and logistically intensive decisions to scale equipment, they can use the inherently flexible and customisable models in the CFD to easily determine the ideal equipment size. By adjusting from small scale to large scale, engineers will be able to determine what size is optimal for a piece of equipment without having to run expensive and long-term physical experiments.
In mining operations, feed is constantly changing, disrupting processes as it goes on. While initial adjustments may work at the start, it is a fluid system that requires adjustments as conditions change. Rather than requiring engineers and technicians to make potentially unsuccessful adjustments in real-time, the CFD can be used to test adjustments so engineers can find the ideal settings as the situation fluctuates and before implementing ineffective changes.
Next Steps
UQ SMI’s next step is to create a proof of concept for the CFD, which will be used to establish an industrially funded collaborative research program. They have secured funding from the Resources Technology and Critical Minerals (RTCM) Trailblazer, a $50million project supported by the federal government’s Department of Education to encourage the translation and commercialisation of university research. UQ SMI intends to jumpstart the collaborative research program with this grant.
The collaborative research program is intended to establish the models for essential emerging technologies. UQ SMI has identified five emerging technologies that would reduce the footprint of current equipment. With industry support, models for all five of these innovations can be established within the CFD.
The identified technologies include:
High voltage pulse pretreatment (HVP)
- Uses lightning to break rocks for preconcentration or preweakening, reducing energy requirements
- Enables feed ore to be sorted by grade
- Generates cracks/microcracks within disintegrated particles, reducing energy requirements for subsequent breakage
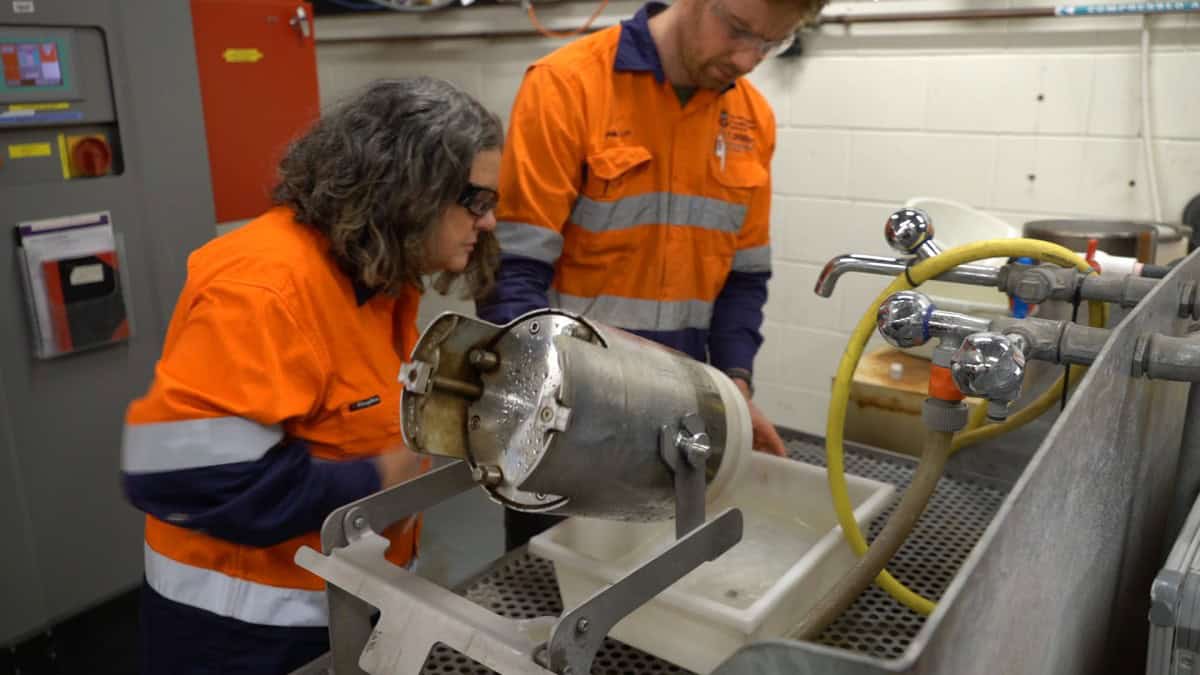
Vertical Roller Mills
- Comminute ore dry, using less energy
- A unit can replace multiple stages of grinding and classification
Inverted hydrocyclones and reflux classifiers
- Changes the physics of the system to improve classification efficiency
- Better classification enables less energy use during grinding by not unnecessarily breaking fines
Fluidised beds and pneumatic high intensity flotation
- Achieves higher recoveries of coarse and fine particles than conventional flotation machines
- Reduction in plant footprint
High-Pressure dewatering rolls and microwave technologies
- Increases dewatering efficiencies to improve handling of tailings, concentrates and backfill
- An enabler of dry stack tailings, a safer more efficient alternative to tailings facilities
- More efficient recycling of water to reduce water consumption
It has taken UQ SMI time to establish the foundation of the CFD, but now that initial experiments have been completed, future models can be more easily added. Because the system relies on universal physics and elements present in existing mining equipment, the model will only need to be expanded to include slight adjustments and additions in each piece of equipment within the CFD.
Currently, the CFD can take weeks to run, but UQ SMI can now use the CFD models to develop faster, more sophisticated flowsheet simulations that are suitable for industry use.
Through their in-house partnership with JKTech, a faster simulation platform can be built from the models. These can eventually be provided to mining companies to run simulations themselves, allowing them to quickly make critical decisions regarding the equipment and processes being used on site.
Industry-involved research
The Julius Kruttschnitt Mineral Research Centre (JKMRC) within UQ SMI has established itself in the mineral process industry through 50 years of contributions of industry solutions. Through collaboration with mining industry stakeholders and research organisations, they have advanced knowledge across the industry. With commercialisation partner JKTech, they intend to realise this knowledge by creating modelling software for the international mining community, so mining companies can be confident in adopting cleaner technologies.
Dr Runge says industry involvement is their key differentiator.
“The JKMRC has a really long tradition of working very closely with the mining industry,” she said.
“We are a little bit different to a lot of other universities because we often do our research funded by industry.
“There is an example where we’ve got a new technology that’s come on board, and we’ve managed to get eight different mining companies to sponsor research work together.
“We have meetings every six months where we present the results and we get mining companies to talk amongst themselves to share learnings from working with those pieces of equipment and putting them into play.
“We act as a bit of a catalyst for pulling mining companies together.”
The Separation Group at UQ SMI aims to get mine sites ready for the energy transition by increasing efficient resource utilisation and decreasing environmental impact by developing methods to allow engineers to test before they invest in expensive, new separations technology. The Separation Group has a history of ongoing industry support from the world’s biggest mining companies, including Newmont, BHP, Rio Tinto and Glencore.
For more information please contact: Associate Professor Kym Runge, [email protected]
or visit the website smi.uq.edu.au/jkmrc